Chisel in hand, Nick Lloyd looks at a piece of wood as Michelangelo once looked upon a large chunk of stone. The objective is to remove just the right amount of raw material to reveal the natural beauty locked inside. Where the Italian Renaissance master sought visual appeal, Lloyd has been on a quest for the perfect tone.
Nestled in the artistic enclave of Northside in the outskirts of Cincinnati, Lloyd works on the bottom floor of a restored 1890 brick house to create some of the world’s most sought after double basses. The third floor is home to his family and the second floor is his showroom of instruments, which have earned the builder numerous awards including first place in the Maker’s Jury category at the 2012 Copenhagen Bass Convention in Denmark.
“Nick’s basses are very musical to play and incredibly versatile,” said Robin Ruscio, a Denver bassist who uses his Lloyd double bass across a variety of jazz and musical theater gigs, most recently in the Broadway tour of Wicked.
“In 2011 I was in the market for a professional quality double bass and wanted a punchier, clearer tone that still retained some richness and depth. I played about 50 basses at the International Society of Basses Convention that year and kept coming back to Nick’s. His was the only bass I was able to pull all of those qualities out of one instrument.”
Size Matters
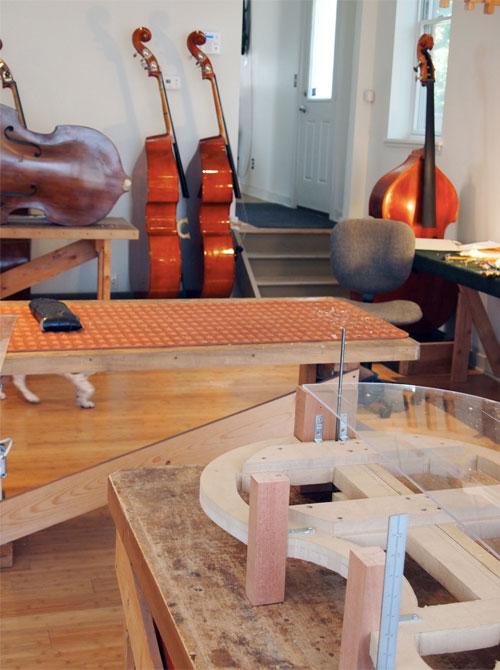
As with other members of the violin family, such as violas and cellos, the double bass has four strings, an ebony fingerboard, and a top of carved spruce. Musicians can pluck the strings with their fingers or use a horse hair bow, techniques called pizzicato and arco respectively, to create a variety of rich tones that mimic the qualities of the human voice.
However, that’s where the similarities stop. While there are dozens of top-notch violin and cello makers, today only a handful of craftsmen endeavor to make an instrument as large as the double bass. A penchant for woodworking, a bottle of glue and a handful of wood clamps will not take you far.
Low-end student models made of pressed wood already start at $2,000. Intermediate-level basses that use a mix of plywood and carved spruce will run between $4,000 and $8,000, while professional quality double basses, which feature solid spruce carved tops along with maple or walnut backs, range from $20,000 to $150,000.
Learning the Craft
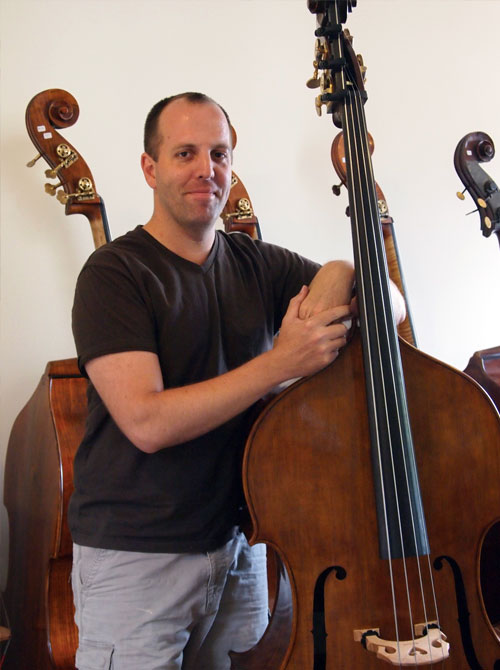
While studying double bass performance at the Longy School of Music in Boston, Lloyd became increasingly interested in the instrument's construction and design in complement to his passion for playing. This curiousity led him to study under such renowned bass luthiers as Michael Shank, Paul Hart, and Daniel Hachez before opening his own shop in Cincinnati in 2000 to begin putting his stamp on upright bass building.
The process of turning raw wood into a finished double bass typically takes Lloyd six weeks. This puts him on track to make around six custom basses a year with a backlog of four months worth of work. He also spends, on average, ten weeks a year delivering and showing basses around the U.S. by car.
Going with the Grain
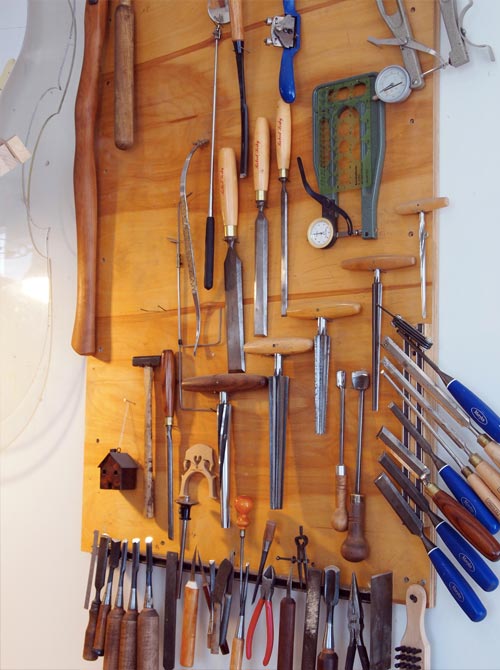
With an instrument that uses wood to transmit the vibrations from the strings to the listener, a luthier relies on different varieties to bring specific sonic qualities to their instruments. For example, maple will produce a brighter tone while less dense wood like walnut elicits a warmer timbre. All woods will mature over time and “open up” as years of playing shape it's tonal color.
Yet, each piece of wood is unique and matching the right wood to the right sound can be more of an art than a science. Grain orientation, tree age, and ultimately construction and design all play a role in determining an instrument's unique tonal properties.
Lloyd studied 100 to 200 year old Italian basses and noted that those made from walnut still had a rich and balanced sound and were in fine structural condition. So in 2005, he started building with walnut backs and sides while keeping the traditional spruce top. The lighter density of walnut allows for the low frequency notes to speak with a fuller tone and play more easily under the bow.
“It’s the nature of wood to respond to it’s environment,” said Lloyd. “That’s why I recommend double basses should be stored in rooms with a humidifier set at 35 percent humidity in the winter months. The wood needs the right amount of moisture. And, as crazy as this might sound, instruments love to be played. I firmly believe the vibrations from the strings condition the wood. It’s why museums hire worldclass musicians to play vintage instruments. Being played is part of that instrument’s maintenance program.”
Looking Forward
After building 30 basses, Lloyd has found that bassists want two sizes for different playing requirements and physical ergonomics. He recently launched two Lloyd Standard Model basses at $32,000, both of which feature a walnut flatback, bookmatched carved spruce top, and seasoned maple neck. One is a 3/4 size with a 40.5inch string length that features a Travel Neck which packs up easily for air travel.
The second is a 7/8 size with 41.5inch string length and a Cextension which is suited for orchestral repertoire or jazz bassists who prefer not to use an amplifier. Both of these basses can be commissioned for $1,000 and are built throughout the year under the watchful eye of Nick's 'quality control officer', Cousin Vern.
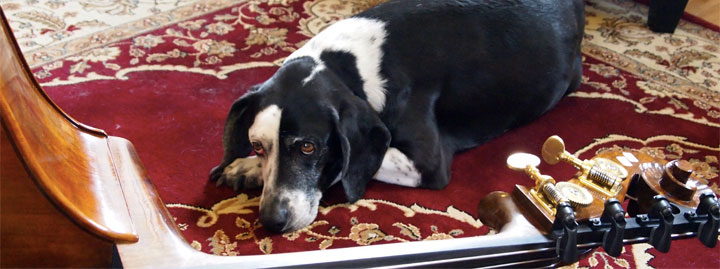